Your cart is currently empty!
In today’s competitive business environment, organizations must continuously refine their processes to enhance efficiency, reduce waste, and improve performance. DMAIC (Define, Measure, Analyze, Improve, Control)—a structured Six Sigma methodology—provides a data-driven approach to optimizing operations and achieving long-term success.
At OptiFlow Strategies, we help businesses harness DMAIC to streamline workflows, enhance quality, and drive sustainable operational excellence.
Understanding the DMAIC Framework
DMAIC is a systematic, five-phase methodology designed to identify inefficiencies, optimize processes, and maintain improvements over time. Each phase serves a critical role in achieving operational excellence:
1. Define: Setting the Foundation for Success
The first step in any process improvement initiative is to clearly define the problem, goals, and expected outcomes. This phase includes:
✔️ Identifying process inefficiencies or quality issues
✔️ Understanding customer and stakeholder expectations
✔️ Establishing project scope and objectives
📌 Example: A manufacturing company struggling with production delays defines its objective as reducing cycle time by 20% within six months.
“Excellence isn’t accidental—it’s engineered. Mastering DMAIC empowers businesses to transform inefficiencies into opportunities for lasting success.”
2. Measure: Quantifying the Problem
In the Measure phase, businesses collect and analyze key performance data to establish a baseline.
This step involves:
✔️ Identifying relevant KPIs and metrics
✔️ Mapping out existing processes to pinpoint inefficiencies
✔️ Gathering quantitative and qualitative data for accurate analysis
📊 Example: A service-based company tracks customer response times and discovers a 30% delay due to workflow bottlenecks.
3. Analyze: Identifying Root Causes
Once data is collected, the Analyze phase focuses on uncovering the root causes of inefficiencies.
Using Six Sigma tools like:
🔹 Root Cause Analysis (5 Whys, Fishbone Diagrams)
🔹 Process Mapping & Value Stream Analysis
🔹 Statistical Data Evaluation
📌 Example: A retail company analyzing customer complaints finds that delayed shipments are caused by inconsistent supplier lead times.
4. Improve: Implementing Targeted Solutions
With insights from the Analyze phase, businesses can implement strategic improvements to eliminate inefficiencies.
This phase involves:
✔️ Developing & testing solutions to optimize processes
✔️ Automating repetitive tasks for efficiency gains
✔️ Training teams on new workflows to sustain improvements
Example: A logistics company reduces order processing time by 40% by automating inventory management.
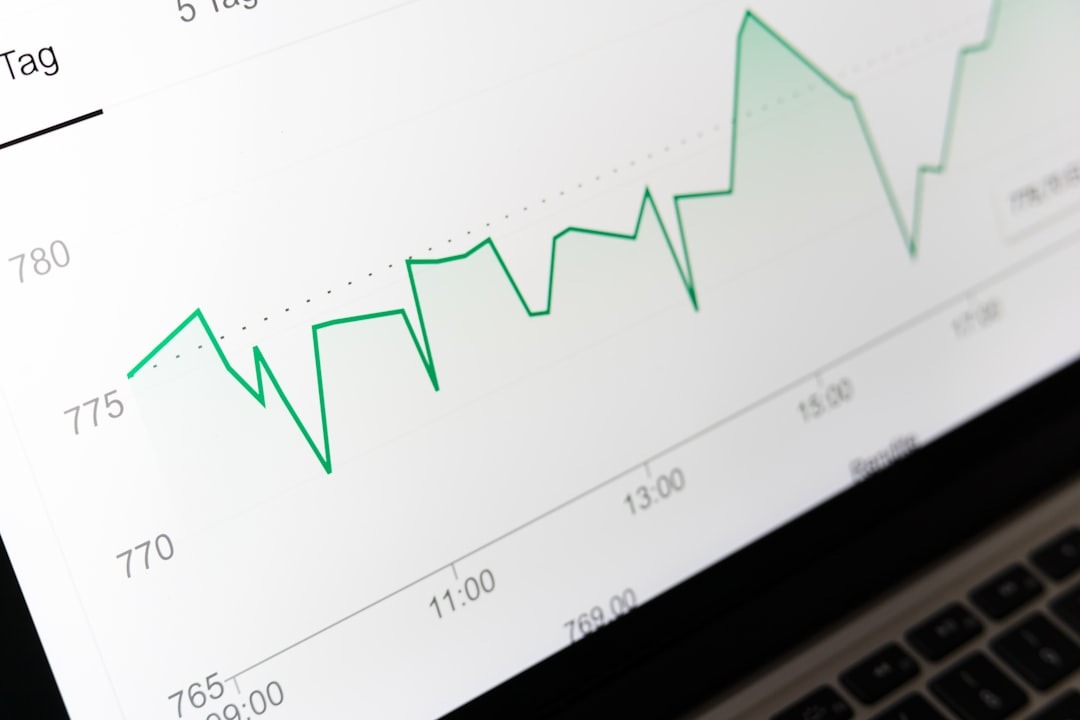
5. Control: Sustaining Long-Term Success
The final step ensures that improvements are maintained and continuously optimized over time.
Businesses implement:
✔️ Ongoing monitoring of KPIs to track success
✔️ Standardized operating procedures (SOPs)
✔️ Regular performance reviews and feedback loops
📌 Example: A healthcare provider sustains a 15% efficiency gain by establishing monthly audits and employee training sessions.
Why DMAIC is Essential for Operational Excellence
Organizations that implement DMAIC effectively experience:
✅ Reduced waste and inefficiencies
✅ Improved customer satisfaction and service quality
✅ Increased profitability through cost savings
✅ Greater agility in responding to business challenges
Whether in manufacturing, healthcare, finance, or service industries, DMAIC provides a proven roadmap for sustainable success.
Drive Operational Excellence with OptiFlow Strategies
At OptiFlow Strategies, we specialize in DMAIC-driven process optimization, helping businesses:
✔️ Identify inefficiencies and implement data-backed solutions
✔️ Enhance operational workflows and team performance
✔️ Develop long-term strategies for continuous improvement
By mastering DMAIC, your organization can transform operations, enhance efficiency, and achieve measurable success.
Ready to elevate your business performance? Contact OptiFlow Strategies today to start your journey toward operational excellence!
Leave a Reply